Plastics are widely used across industries because they are lightweight, cost-effective, and highly versatile. However, many people believe plastics cannot withstand high temperatures. In reality, heat-resistant plastics have been developed to perform in extreme conditions while keeping their mechanical and thermal properties.
Identifying what makes a plastic heat-resistant is essential when choosing the right material for high-temperature applications. This guide explores the factors behind heat resistance, the best high-temperature plastics, and how industries are using these materials in specialized applications.
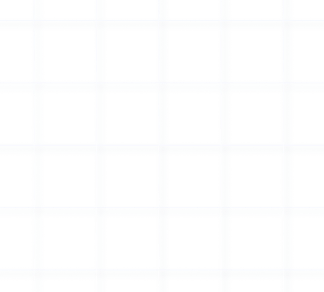
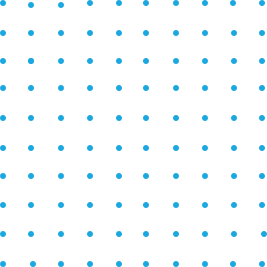
An Expert is just around the corner.
With over 100 years of combined product knowledge and industry experience, we are confident our plastics experts can help you find a solution for your application.
What Makes Certain Plastics Heat-Resistant?
Heat resistance in plastics depends on their molecular structure and any reinforcements or additives used. Some plastics soften gradually when exposed to high temperatures, while others maintain their strength up to a defined melting point.
There are two main categories of plastics:
Amorphous plastics (such as PEI, PSU, and PVC) soften gradually instead of having a clear melting point. This makes them ideal for applications requiring stability under heat.
Semi-crystalline plastics (such as PEEK, PTFE, and PPS) have a more rigid structure and maintain their properties at higher temperatures, making them suitable for demanding environments.
To measure a plastic’s ability to withstand high temperatures, several key thermal properties are considered, including:
-
Continuous Service Temperature (DGT)
The maximum temperature at which a plastic retains at least 50% of its properties after long-term exposure.
-
Heat Deflection Temperature (HDT)
The temperature at which a plastic begins to deform under load.
-
Glass Transition Temperature (Tg)
The point where an amorphous plastic transitions from rigid to rubbery.
-
Flame Resistance (UL 94 Rating)
Indicates how well a plastic resists ignition and burning.
Top Heat-Resistant Plastics and Their Performance
Different plastics offer varying levels of heat resistance. Thermoplastics such as PEEK, PTFE, and PEI can soften when heated but still maintain their properties within their operating temperature range. Due to their strength, chemical resistance, and ability to handle high heat, these materials are often used in aerospace, medical, and industrial applications.
PEEK, for example, can handle continuous temperatures up to 482°F (250°C) and is known for its outstanding mechanical and chemical resistance. PTFE (commonly known as Teflon) has a maximum service temperature of 500°F (260°C) and is widely used for its low friction and chemical inertness. Meanwhile, PEI (Ultem) remains stable at 340°F (171°C) and is valued for rigidity and flame resistance.
Thermosets, on the other hand, offer even greater heat resistance due to their permanently cross-linked molecular structure, which prevents softening or melting under high heat. For example, Vespel, a polyimide material, can withstand temperatures up to 572°F (300°C) without losing its properties. Torlon, a polyamide-imide, retains its strength at 500°F (260°C) and is commonly used for powertrain components and coatings.
Comparison of Top Heat-Resistant Plastics
Material | Max Continuous Temp (°F/°C) | Key Properties | Applications |
---|---|---|---|
PTFE (Teflon®) | 500°F (260°C) | Low friction, chemical resistance | Bearings, seals, non-stick coatings |
PEEK | 482°F (250°C) | High strength, chemical, and wear resistance | Aerospace, automotive, medical |
PEI (Ultem®) | 340°F (171°C) | Rigid, flame-resistant, good electrical properties | Electronics, healthcare, chemical processing |
PPS (Ryton®) | 428°F (220°C) | Electrical insulation, corrosion-resistant | Industrial electrical connectors |
Vespel® | 572°F (300°C) | Non-melting, no outgassing | Jet engines, industrial machinery |
Torlon® | 500°F (260°C) | High creep resistance, wear-resistant | Powertrain components, coatings |
Industry Applications of Heat-Resistant Plastics
Heat-resistant plastics are vital in many industries, each requiring specific properties to guarantee optimal performance and durability. These plastics are increasingly replacing metal components in the aerospace and automotive sectors. Their ability to withstand extreme heat while being significantly lighter helps improve fuel efficiency and reduce overall weight. Engine components, insulators, and structural reinforcements from heat-resistant plastics allow these industries to innovate without compromising safety or performance.
High-temperature plastics are used in sterilizable surgical instruments, medical device housings, and laboratory equipment in the medical and pharmaceutical fields. Many of these materials, such as PEEK and PPSU, can endure repeated sterilization cycles without degrading, making them ideal for environments that require strict hygiene standards.
The electronics and electrical industries depend on heat-resistant plastics for insulation and structural integrity. Materials like PEI and PPS are commonly used in circuit boards, connectors, and enclosures that must endure prolonged heat exposure without warping or losing electrical insulating properties. As electronics become more compact and powerful, the demand for durable, heat-resistant materials is only growing.
In food processing, plastics that can endure high temperatures are necessary for machinery components that come into direct contact with hot food or steam. Heat-resistant polymers ensure that conveyor belts, mixing paddles, and processing equipment maintain structural integrity and safety compliance under extreme operating conditions.
Using Additives and Modifications
Specialized additives and reinforcements can further improve heat-resistant plastics. By modifying their composition, manufacturers can enhance specific properties such as durability, stability, and friction resistance, making them more suitable for demanding applications.
Here’s how:
Lubricants (PTFE, Graphite)
These additives reduce friction and improve wear resistance, making plastics ideal for components exposed to constant motion and heat, such as bearings and sliding surfaces.
Reinforcements (Glass & Carbon Fiber)
Adding glass or carbon fibers increases stiffness, thermal stability, and dimensional accuracy, helping to prevent warping under extreme temperatures.
Coatings and Composite Additives
Applying protective coatings or incorporating composite additives extends the lifespan of plastic components by adding an extra layer of heat protection, ensuring they remain functional in high-temperature environments.
Picking the Right Heat-Resistant Plastic
Finding the best heat-resistant plastic requires careful consideration of several factors. The operating temperature is important, as the material must align with the application's heat exposure requirements to ensure long-term durability.
Mechanical strength is also crucial, as some applications require plastics that can withstand heavy loads and constant stress. Additionally, chemical resistance is important for applications where the plastic may come into contact with solvents, oils, or acids.
The manufacturing process also plays a role in determining the right plastic. Some materials, such as PEEK, PTFE, and PPS, are best suited for machining, while PEI and PPS are more commonly used in injection molding. For advanced applications, 3D printing with high-performance resins can provide viable solutions for heat-resistant components.
Finally, cost and availability must be considered. While premium materials like PEEK and Vespel offer exceptional heat resistance, they are more expensive. More budget-friendly alternatives, such as PPS and PEI, provide reliable heat resistance at a lower cost.
Key Takeaways
Heat-resistant plastics are changing industries by offering durable, lightweight, high-performance alternatives to metals and ceramics. Whether used in aerospace, medical, or industrial applications, these materials provide long-lasting solutions for extreme environments. As technology continues to evolve, new high-temperature polymers will further expand the possibilities of what plastics can achieve in modern engineering.
Discover More Details
For expert guidance on selecting the right heat-resistant plastic for your application, contact Piedmont Plastics to learn more about our products and solutions!
Get In Touch