What Plastics Are Best For Hot Temperatures?
When specific industries or processes regularly use high temperatures, it’s important for the plastic parts being used to maintain their strength and durability. That’s where heat-resistant plastics come in. These plastics are designed to function continuously at temperatures higher than 300ºF without losing their characteristics.
But there is more to selecting a suitable heat-resistant plastic material than operating temperature. Chemical resistance, friction and wear performance, and tensile strength must also be considered.
Below are some of the top heat-resistant plastics suitable for the most demanding applications found in manufacturing and processing.
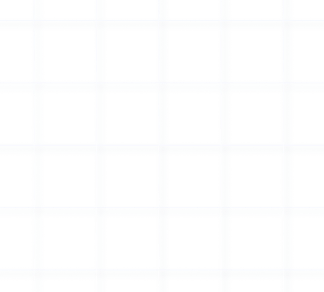
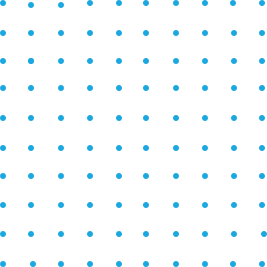
An Expert is just around the corner.
With over 100 years of combined product knowledge and industry experience, we are confident our plastics experts can help you find a solution for your application.
Polytetrafluoroethylene (PTFE)
Discovered in 1938, polytetrafluoroethylene (PTFE)—also known as Teflon—is a versatile material often used as a non-stick coating for cookware due to its ability to remain bonded to a surface while also undergoing intense heat. PTFE is also used as a lining for containers and pipes due to its ability to withstand corrosive chemicals.
PTFE melts at 620°F yet also remains strong at -450°F. Due to the high processing temperatures involved in its manufacture, PTFE can be more pricey than other materials.
Polyetheretherketone (PEEK)
Polyetheretherketone (PEEK) enjoys excellent mechanical and thermal characteristics. It’s employed in severe conditions as a metal substitute or replacement because of its strong, rigid, and durable qualities. Bearings, pumps, medical devices, and aircraft components employ PEEK.
PEEK is heat resistant, can withstand 482°F continuously, 590°F briefly, and melts at 649°F. As a result, PEEK is a popular thermoplastic for various industries because of its outstanding thermal and mechanical strength.
Polyamide-imide (PAI)
Polyamide-imide (PAI), also known as Torlon, is a high-performance thermoplastic and serves as a high-temperature, high-wear alternative to metal. In addition, PAI resists creep and acids, making it perfect for harsh settings, and it is a choice material for aerospace, propulsion, and automotive components.
PAI’s heat resistance makes it ideal for high-temperature applications that expose it to constant temperatures of up to 500°F and occasionally to 527°F. In addition, PAI’s flame resistance makes it self-extinguishing within 10 minutes. On the lower end, PAI can withstand temperatures as low as -238°F without becoming brittle.
Vespel
DuPont’s Vespel polyimide is used in industrial machines, cars, and aerospace technology. It is highly heat-resistant and has no melting point. Vespel can withstand continuous temperatures of 442°F, 572°F of repeated heat, and bursts of 899.6°F without losing integrity. Vespel will only lose integrity after outgassing–most often oxygen.
In low-temperature applications, Vespel can withstand -240°C without turning brittle.
Polyetherimide
Polyetherimide, also known as Ultem, is a semi-transparent, high-strength plastic ideal for high-temperature uses. Despite a high melting point at 426°F, it boasts the highest dielectric strength of any thermoplastic and is ideal for circuit boards, high-temperature lighting, engine components, and 3D printer bed materials.
Polyetherimide is similar to PEEK in some ways but has a lower impact strength and useable temperature. On the other hand, this material is less expensive than PEEK, making it a reasonable choice when cost control overrides durability concerns.
Polyphenylene Sulfide (PPS)
Polyphenylene sulfide (PPS) can be molded, extruded, and machined to precise tolerances. Since 1983, it’s been used to make chemical- and heat-resistant synthetic fibers and fabrics for electrical insulation, film capacitors, fuel and brake systems, heat shields, and more.
PPS can withstand temperatures up to 424°F and won’t dissolve in solvents below 392°F. It can also withstand 536°F without melting. While PPS is widely known and valued for its heat resistance, it also passes UL94V-0 standards without adding flame-retardant materials.
Polysulfone (PSU)
Like polycarbonate, polysulfone (PSU) remains robust and stable at high temperatures. Engineers turn to polysulfone as the best alternative when polycarbonate’s strength isn’t enough. It possesses a high service temperature, high-temperature endurance, and inherent flame retardancy.
Due to PSU’s characteristics, it is often used in electrical equipment, vehicle manufacturing, and medical technology. Its melting point is over 932°F, making melting difficult to heat-process. PSU maintains its impact resistance between -212°F and 203°F but will gradually weaken outside this range.
Heat Resistant Plastics at Piedmont Plastics
Different engineering and manufacturing challenges will require various plastics for the best performance and reliability. For example, heat-resistant plastics may be needed for high-temperature applications, but additional factors are often at play. One plastic may be preferred for particular applications due to certain physical features, chemical resistance, or budgetary restrictions, whereas other plastics would not be as nearly suitable.
For this reason, it’s essential to consider every aspect of your engineering, manufacturing, or processing project when selecting a suitable heat-resistant plastic. Contact the materials experts at Piedmont Plastics to help find the best material for your project.
Heat Resistant Plastics at Piedmont Plastics
With numerous distribution centers across North America, Piedmont Plastics is in a perfect position to help with any production solution. Contact us today for more information.
Contact Us