Ensuring Longevity in Harsh Environments
Chemical-resistant plastics are essential for products used in harsh environments, with their durability determined by the chemical concentration, temperature, and exposure time; popular options include Polypropylene, PTFE, PEEK, and PVDF, each with distinct resistance properties and applications.
Durability is a vital part of choosing plastics when making products for harsh environmental conditions. When plastics resist damage from acids, bases, solvents, and other harsh chemicals, they tend to stand up well under all conditions. Here is a closer look at what chemical resistance means and what materials are the most chemically resistant.
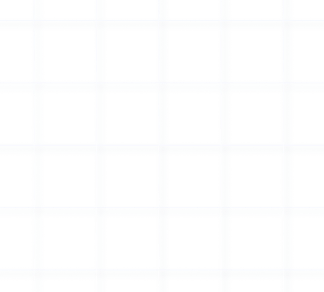
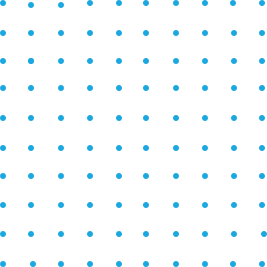
An Expert is just around the corner.
With over 100 years of combined product knowledge and industry experience, we are confident our plastics experts can help you find a solution for your application.
Chemical Compatibility Explained
Chemical compatibility refers to whether plastic is compatible to use with a particular chemical. In other words, if the plastic is exposed to that material, will the plastic lose integrity? Chemical compatibility is a key metric when deciding chemical resistance. Many factors can impact whether a plastic reacts to a particular chemical, so testing needs to be done in a controlled environment.
Often, chemical compatibility is tested by exposing plastic to a material constantly for 30 days at a set temperature. Then, the effect of the exposure is evaluated or measured. The plastic will then be given a rating regarding that chemical. The less damage to the plastic, the higher the chemical resistance rating.
Key Considerations for Chemical Resistance
Several factors impact chemical resistance. First, the chemical concentration can affect how well a plastic resists damage. Some plastics may withstand small concentrations of a particular solvent but not large concentrations of a specific chemical.
Temperature can also impact chemical resistance. Testing is done at a set temperature, but a higher or lower temperature can make the plastic more or less susceptible to damage from the chemical.
Additives in the plastic can change its chemical resistance. Sometimes, polymers can have an additive that changes the chemical resistance to make the plastic work for a particular application.
Finally, exposure time can impact damage. The damage won’t appear instantly, and some plastics take longer to show signs of damage.
In light of these factors, four popular plastics are highly resistant to damage from popular solvents.
1. Polypropylene (PP)
This low-cost polymer doesn’t crack easily and is resistant to chemical damage. It withstands alcohol, bases, and diluted acids well. It also has good resistance to hydrocarbons, aldehydes, esters, and ketones, though not as strong as the first three. It has a low melting point, which makes it easy to form through injection molding. Common applications include:
Industrial tanks and pipes
Consumer goods
Fibers and fabrics
2. PTFE (Polytetrafluoroethylene)
PTFE is known by the brand name Teflon. This fluoropolymer has one of the best chemical resistance ratings of all plastics. It can handle extremely low temperatures and has a low coefficient of friction. It’s also only susceptible to damage from organic halogenated compounds, such as oxygen difluoride or chlorine trifluoride. Common applications include:
Medical implants and grafts
Automotive parts, including power steering systems and seals
Chemical industry equipment, such as autoclaves and tanks
Engineering non-stick surfaces, tanks, and containers
Electrical and electronic insulation and circuit boards
3. PEEK (Polyetheretherketone)
This semi-crystalline, high-performance thermoplastic is a rigid plastic that resists damage from harsh chemicals. It’s an older product, coming to market in the 1980s, with high resistance to wear, high temperatures, and fatigue. Common applications include:
Electronics, including mobile phone cases and laptop computers
Healthcare equipment, including teeth and load-bearing implants
Aerospace engine parts and exterior parts to resist weather exposure
4. PVDF (Polyvinylidene Fluoride)
Finally, PVDF is another semi-crystalline thermoplastic with high chemical resistance. It’s also non-flammable and UV resistant. This plastic resists organic acids, aromatics, alcohols, and halogenated solvents but doesn’t resist strong bases and ketones very well. Common applications include:
Industrial gaskets and seals
Electrical wires and cables
Electronics, including components of lithium-ion batteries
Filtration equipment and tubing
Choosing the Right Chemical-Resistant Plastics
The main factor to consider when choosing a chemical-resistant plastic is the type of solvent it will need to handle. Each of the plastics mentioned above reacts differently depending on the solvent it’s exposed to, and thus you will need to choose a plastic that fits your application.
The other properties of the plastic, such as its machinability, temperature and weather resistance, or rigidity, can all play a role. You must also consider whether you need UV resistance if the plastic will be in a high-temperature environment and if moisture is a problem. Choose a plastic that resists the solvent you need and fits the other factors in the environment where it will be used. Piedmont Plastics can help you determine which plastic material best suits your needs based on your specific applications.
Best Practices for Maintaining Chemical Resistance
In addition to choosing the right plastic for your application, you must properly care for it to ensure it retains its chemical-resistant properties.
First, use caution in how you clean these materials. Most of them can be properly cleaned with a non-caustic detergent and water, but make sure the detergent is not a chemical compound that will cause damage to the plastic. Never scour or use abrasive cleaners on these plastics, as they could damage the surface and make them more prone to chemical damage. Always consult with the manufacturer’s recommendations for cleansers to use when cleaning these products.
Unless the plastic is designed for outdoor use, avoid exposing it to the elements for long periods. UV damage and temperature fluctuations can cause chemical resistance to break down. Store them in a secure, indoor environment if possible.
With the right handling, cleaning, and storage, chemical-resistant plastics should retain their resistance for a long time. If you need chemical-resistant plastic materials and are still determining what product will best meet your needs, contact the Piedmont Plastics team for help.
Buy Chemical-Resistant Plastics At Piedmont Plastics Today!
Piedmont Plastics is your source for mechanical plastics that will withstand the harshest of chemicals. Contact your local Piedmont Plastics branch today to talk with our plastic experts about which material would work best for your applications.
Get In Touch