Advancing Plastic Fabrication
Plastic manufacturing is transforming with groundbreaking innovations reshaping the industry. The landscape of plastic manufacturing is evolving rapidly with sustainable fabrication methods for widely used plastics. These advancements are streamlining production processes and aiming to make them more eco-friendly and versatile. In this article, we will explore the latest innovations in plastic manufacturing and their impact on key industries.
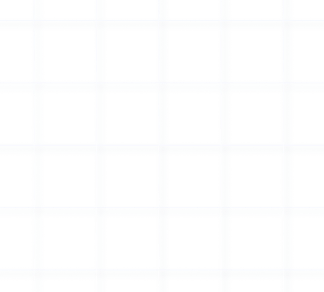
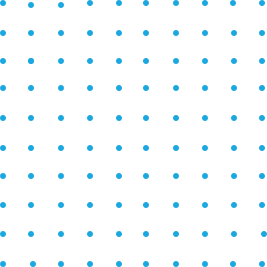
An Expert is just around the corner.
With over 100 years of combined product knowledge and industry experience, we are confident our plastics experts can help you find a solution for your application.
Automated Fabrication of High-Demand Plastics
Automation has revolutionized the plastic fabrication industry, enabling manufacturers to streamline production processes and meet the growing demand for widely used plastics. By integrating advanced automation technologies, manufacturers can enhance efficiency and precision in every step of the fabrication process.
Automation allows for streamlined part insertion/extraction, trimming/cutting, quality control checks, and post-secondary operations like assembly and packing. This increases production capacity and ensures higher quality control, reducing the margin of error in fabricating custom plastics for industries such as medical and automotive.
For example, detectable plastic materials are used in conveying equipment. When applied to food supply industries, this helps inspectors find unwanted particulates in food products. This automation process also applies when ensuring plastic products (like food storage bins) meet FDA compatibility.
Manufacturers can significantly reduce cycle times and enhance real-time production monitoring by automating fabrication processes. This ensures consistent product quality and meets the needs of a dynamic market reliant on efficient and reliable supply chains.
Sustainable Fabrication Methods for Common Plastics
Between 1990 and 2017, patents for environmentally relevant plastics technologies rose significantly, with a particular focus on recycling technologies. This trend showcases a shift towards more sustainable practices driven by increased consumer environmental awareness and policies like extended producer responsibility.
Piedmont Plastics has won environmental excellence awards from the IAPD (International Association for Plastics Distribution). Our team achieves this by investing heavily in reusing plastic materials. Two examples are The Falconboard® Eco Digital Sheet and Spartech PETG Sheets.
Other Examples of Sustainable Practices
- Bioplastics: Like PLA and PHAs (Polyhydroxyalkanoates)
- Recyclable Plastics: Like HDPE and PET
- Biodegradable Additives: Include Vegetable, cellulose, and oil-based materials.
- Sustainable Sources: Like using renewable resources and reducing waste during different supply chain stages.
- Upcycling: Turning old plastic into new plastic
- Composting: Breaking down organic material for re-use.
The increasing recognition of the environmental impact of plastics and the growing demand for sustainable options have led to innovative fabrication methods aimed at eco-friendly processing of commonly used plastics. These advancements play a significant role in reducing the carbon footprint of the plastics industry and addressing the challenge of plastic waste in our daily lives.
New Molding Technologies
Remarkable advancements have been made in plastic fabrication molding techniques for materials such as PVC and polycarbonate. These innovations have revolutionized manufacturing, increasing efficiency and reducing operational costs.
One significant outcome of these advancements is the development of more versatile and durable products using PVC and polycarbonate, catering to a wide range of industries. These materials can now fulfill various application needs, offering exceptional strength and flexibility.
Moreover, introducing new molding technologies has enabled the production of intricate and complex designs. Manufacturers can now meet the demand for more customized and sophisticated plastic products. This development has opened doors for endless possibilities and greater creativity in product design.
Another crucial aspect of these new molding technologies is the improved quality and precision of final products. The advancements contribute to the overall enhancements in performance and functionality, ensuring that the end products meet the highest standards.
The plastic manufacturing industry is witnessing a significant shift with the growing adoption of these advanced molding techniques for PVC and polycarbonate. These technologies reshape the industry's capabilities, enabling innovative and sustainable solutions across various applications.
Impact of Fabrication Innovations
In recent years, the plastics industry has witnessed a remarkable transformation with the introduction of advanced fabrication methods. These innovations are revolutionizing the use of popular plastics in key industries such as healthcare and automotive, leading to significant improvements in product performance and sustainability.
In the healthcare industry, advanced fabrication techniques have paved the way for developing highly customized and precise medical devices and equipment. This has elevated the standards of patient care, allowing for more accurate diagnoses and effective treatments. Furthermore, integrating new molding technologies has streamlined the manufacturing process of plastic parts, reducing production cycle times and improving overall product quality.
Moreover, these fabrication advancements have facilitated the creation of biocompatible and sterilizable plastic materials for critical medical applications. This has significantly elevated safety standards in healthcare settings.
Similarly, in the automotive sector, innovative fabrication methods enhance the production of lightweight and durable plastic components. This, in turn, contributes to improved fuel efficiency and overall vehicle performance. Replacing parts with high-durability plastic is much easier, leading to stronger and cheaper materials than metal.
It is worth noting that adopting sustainable and eco-friendly processing methods for popular plastics has become increasingly important in the healthcare and automotive industries. Fabrication innovations align with the growing environmental awareness and regulatory requirements, ensuring a reduced carbon footprint and a more sustainable approach to plastic production.
Get In Touch
The impact of fabrication innovations on industry staples like plastics cannot be overstated. These advancements are transforming the use of popular plastics in key sectors, resulting in improved product performance, enhanced sustainability, and heightened safety standards.
Contact Us To Learn More