Piedmont Plastics is a leading supplier of high-performance engineering thermoplastics designed for the demanding conditions of the oil and gas industry. From petrochemical refining to oil and gas exploration, our advanced plastic materials provide durable, cost-effective, and corrosion-resistant solutions for detailed applications such as oil refining, fracking, pumping, and sub-sea systems.
As the industry looks to improve efficiency, longevity, and safety, high-performance thermoplastics are becoming increasingly central in oil and natural gas transportation and processing.
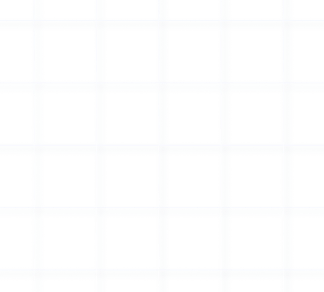
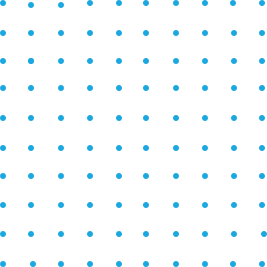
An Expert is just around the corner.
With over 100 years of combined product knowledge and industry experience, we are confident our plastics experts can help you find a solution for your application.
The Need for Advanced Materials in Oil and Gas Applications
Oil and gas operations expose materials to extreme temperatures, high pressures, corrosive chemicals, and abrasive environments. While strong, traditional metals are often susceptible to corrosion and mechanical wear, leading to increased maintenance costs and downtime. With their exceptional chemical resistance, lightweight nature, and superior wear properties, thermoplastics are emerging as essential alternatives for many significant components.
Engineering thermoplastics can withstand the harsh conditions of offshore drilling rigs, petrochemical processing plants, and oilfields, ensuring equipment longevity and reliability. These materials significantly extend the operational lifespan of components that would otherwise deteriorate under the challenging conditions found in oil and gas production environments.
Common Plastics for Oil and Gas Applications
PEEK (Polyetheretherketone)
PEEK is a high-performance thermoplastic known for its remarkable chemical resistance, high-temperature tolerance, and superior mechanical properties. As a result, this material is particularly suited for applications that require dimensional stability under high-stress conditions.
PEEK keeps its integrity even in environments exposed to steam, salt water, and hydrocarbons, making it an excellent choice for:
Downhole drilling tools
Valve seats
Seals and gaskets
Wear-resistant components
PTFE (Polytetrafluoroethylene)
PTFE, commonly known as Teflon®, is widely used in the oil and gas sector due to its low coefficient of friction, high chemical resistance, and excellent thermal stability.
Available in sheets, rods, and tubes, PTFE is ideal for:
Bearings and bushings
Seals and gaskets
Valve seats
Thrust washers
Downhole drilling tools
Phenolic Materials
Phenolic materials are lightweight, mechanically tough, and resistant to impact, friction, and chemical corrosion. These properties make them ideal for electrical insulation and structural applications in oil and gas equipment.
Their durability and cost-effectiveness have led to their adoption in:
Bushings
Thrust washers
Gaskets
Spacers
Rings and collars
Cast Nylon
Cast nylon is known for its toughness, impact resistance, and excellent wear characteristics. It is a cost-effective solution for many oil and gas applications due to its ability to withstand significant mechanical loads while maintaining a low coefficient of friction.
Cast nylon components can be easily machined into complex shapes for:
Bearings and bushings
Seals and gaskets
Thrust washers
Valve seats
Polycarbonate
Polycarbonate is a transparent thermoplastic with outstanding impact resistance, dimensional stability, and dielectric properties. It is also highly resistant to moisture absorption and flame retardant, making it an excellent material for protective barriers and enclosures in industrial environments.
Common applications include:
Safety partitions
Heavy equipment glazing
Transporting Other Liquids
Beyond oil and gas, engineering thermoplastics are crucial in transporting a wide range of liquids across various industries. Their superior chemical resistance, durability, and adaptability make them ideal for handling aggressive fluids, industrial chemicals, potable water, and high-purity liquids.
In chemical processing industries, thermoplastics such as PTFE, PEEK, and UHMW (Ultra-High Molecular Weight Polyethylene) are used in piping systems and storage tanks for safely transporting acids, bases, and solvents, preventing degradation and reducing maintenance downtime. For municipal water treatment and wastewater management, materials like HDPE (High-Density Polyethylene) and CPVC (Chlorinated Polyvinyl Chloride) are widely utilized due to their resistance to biofouling, chlorine, and other treatment chemicals, ensuring longevity and corrosion resistance. In the food and beverage sector, FDA-compliant PTFE and polycarbonate enable the safe transport of dairy, fruit juices, and alcoholic beverages, maintaining sanitary conditions and resisting thermal stress.
Similarly, the pharmaceutical and medical industries rely on sterile, non-reactive thermoplastics like PFA (Perfluoroalkoxy) and polycarbonate for transporting high-purity liquids used in bioprocessing, laboratory equipment, and medical-grade tubing, ensuring product integrity and preventing contamination.
Advantages of Using Plastics in the Oil and Gas Industry
The use of engineering thermoplastics in oil and gas applications offers several key advantages over traditional materials:
Corrosion Resistance
Unlike metals, plastics do not rust or degrade when exposed to harsh chemicals, salt water, or hydrocarbons.
Lightweight Construction
Plastics are significantly lighter than metals, reducing transportation and installation costs while improving equipment efficiency.
Extended Lifespan
Thermoplastics offer superior wear resistance and mechanical strength, leading to reduced maintenance and longer service life.
Low Friction and Self-Lubrication
Many plastics exhibit excellent sliding properties, reducing energy consumption and improving equipment performance.
Thermal and Electrical Insulation
Plastics provide effective insulation against extreme temperatures and electrical conductivity, ensuring safer operation in high-risk environments.
Cost Efficiency and Sustainability
As the oil and gas industry continues to evolve, sustainability and efficiency have become primary concerns. Engineering thermoplastics are critical to minimizing material waste, reducing energy consumption, and lowering overall operational costs.
Additionally, plastics allow for design flexibility, enabling the production of lightweight, high-strength components that outperform traditional alternatives in demanding applications.
Let’s Work Together
Piedmont Plastics is committed to supplying high-quality engineering thermoplastics for oil and gas transportation and processing. As the industry moves towards greater efficiency, safety, and environmental responsibility, our plastic materials offer the durability, reliability, and cost-effectiveness necessary to meet these challenges.
By leveraging advanced thermoplastic solutions, oil and gas companies can optimize their operations, reduce maintenance costs, and enhance equipment longevity in even the harshest conditions.
Learn More
Looking for further insights? Give us a call or send us a message to see how we can help you!
Contact Us