Leveraging Advanced Plastic Materials to Create Safer Workplaces
Whether you manage a manufacturing facility, process sensitive materials like food or pharmaceuticals, or oversee an automated distribution center, reducing accidents and minimizing downtime are part of your daily job. As safety concerns grow, advanced plastic materials, such as impact-resistant machine guards and anti-slip flooring, have emerged as indispensable tools.
Unlike metals or glass, polycarbonate, HDPE, and PETG plastics are lightweight, durable, and corrosion-resistant. These characteristics make them uniquely suited to safeguarding both workers and products, especially in settings that demand consistency, cleanliness, and cost-effectiveness.
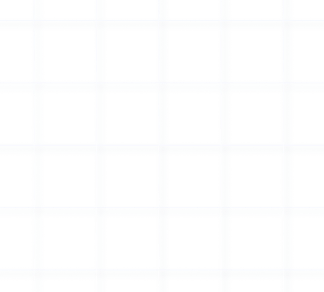
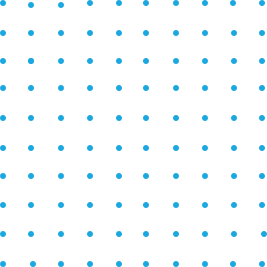
An Expert is just around the corner.
With over 100 years of combined product knowledge and industry experience, we are confident our plastics experts can help you find a solution for your application.
An Overview of Key Safety Plastics
When choosing materials for industrial safety solutions, it's essential to understand how different plastics perform under specific conditions. Each type of plastic has unique properties that make it suitable for safety applications.
Facility managers can ensure optimal performance by selecting the right material while addressing specific environmental and operational hazards. Here’s a breakdown of commonly used plastics and their strengths:
Polycarbonate: Exceptional impact resistance and optical clarity, perfect for safety windows and machine guards.
HDPE (High-Density Polyethylene): Its high strength-to-weight ratio and excellent chemical resistance make it ideal for heavy loads and frequent cleaning.
PETG and Acrylic: A versatile choice that balances clarity and durability, offering a cost-effective alternative for many industrial settings.
PVC and Vinyl: Flexible and flame-resistant options suitable for adaptable and fire safety applications.
Machine Guards
Machine guards are a first line of defense against injuries from moving parts, debris, or sudden equipment malfunctions. Regulations such as those from OSHA and ANSI often call for robust materials that can withstand repeated impacts. Polycarbonate, in particular, offers exceptional visibility and structural integrity, allowing operators to observe internal processes without compromising safety.
HDPE or specialized polycarbonate grades can keep their shape and functionality under stress in high-temperature or chemically aggressive environments. These plastics are easy to form, machine, and customize, which makes it simpler to create guards that fit precisely around complex machinery.
Barriers and Fencing
Industrial operations often require permanent barriers for ongoing hazards and movable barriers for short-term tasks like maintenance. Rigid barriers can include plastic railings or panels that resist corrosion, stay lightweight, and require little upkeep. Some workplaces also use sensor-based light curtains housed in plastic enclosures to halt machinery when the beam is disrupted, thus providing a softer yet highly responsive layer of protection.
Because plastics resist warping, rust, or dents, they are well-suited to high-traffic zones where frequent contact occurs. They also tend to clean easily, a critical factor in facilities with intense hygiene demands, such as food processing or pharmaceuticals.
Safety Mats and Anti-Fatigue Flooring
Mats play a large role in the industrial workplace by reducing slip-and-fall risks, decreasing worker fatigue, and protecting floor surfaces. HDPE mats, for instance, can offer a stable, durable surface resistant to UV and temperature fluctuations, making them a natural choice for areas where equipment or foot traffic is constant.
Meanwhile, PVC or rubber blends offer added cushioning for workers who must stand for extended periods, reducing strain and increasing productivity. Plastics are easy to install and move, allowing plants to reconfigure workstations without significant downtime or heavy lifting equipment.
Regulatory Compliance and Industry Standards
Industrial facilities must meet safety regulations that differ across sectors, and selecting the right materials is critical for compliance. Plastics like polycarbonate and HDPE often meet or exceed impact-resistance requirements set by OSHA and ANSI. In food production, FDA-compliant materials ensure that safety measures align with hygiene standards, while fire-retardant plastic formulations help facilities in high-risk areas meet UL or NFPA codes.
Facilities can avoid penalties, reduce liability, and create a safer workplace by choosing materials that align with these standards. Important regulatory considerations include:
Impact Resistance: Polycarbonate and HDPE meet OSHA and ANSI requirements for durable and reliable safety guards.
Food Safety: FDA-compliant polycarbonate, PETG, and HDPE grades prevent contamination in food production environments.
Fire Safety: Fire-retardant plastics support compliance with UL and NFPA codes in high-risk areas.
Liability Reduction: Adhering to safety standards minimizes risks and fosters a secure working environment.
Trends in Safety Plastics
As technology evolves, advanced coatings and design features continue to enhance the capabilities of industrial plastics. Abrasion-resistant or anti-static finishes extend the lifespan of plastics in high-wear environments. Embedding sensors or RFID tags directly into machine guards can enable real-time equipment performance tracking, providing another layer of transparency and control.
Additionally, as sustainability becomes more critical, closed-loop programs allow facilities to recycle or repurpose used plastics like polycarbonate or HDPE, contributing to a more circular economy.
Why Partner with Piedmont Plastics
Piedmont Plastics offers a broad portfolio of materials, including polycarbonate, HDPE, PETG, acrylic, and PVC, ensuring a precise match for different mechanical or chemical demands. Our technical expertise allows us to guide customers in choosing the right plastics while meeting industry regulations such as FDA and OSHA. Since materials can be fabricated to custom shapes and sizes, our team supports standard and specialized applications, including machine guards, barriers, and flooring.
We maintain ample inventory through a reliable supply network to avoid production delays. Moreover, many of our materials come in eco-friendly or recyclable options, aligning with environmental goals.
Other Plastics Used for Safety Barriers
In addition to commonly used plastics like polycarbonate, HDPE, and PETG, several other materials bring unique benefits to industrial safety and operational needs. These specialized plastics address challenges in environments requiring resistance to wear, chemicals, or extreme temperatures. By exploring additional options, businesses can unlock innovative solutions tailored to specific industries.
Examples include:
Nylon (PA): Is ideal for applications requiring wear resistance and low friction, such as bushings, gears, and conveyor components.
PTFE (Polytetrafluoroethylene): Is known for exceptional chemical resistance and non-stick properties, rendering it perfect for seals, linings, and extreme temperature environments.
ABS (Acrylonitrile Butadiene Styrene): Provides impact resistance and rigidity, making it suitable for lightweight equipment housings and barriers.
Let’s Make The World a Safer Place Together
Safety plastics aren’t just about meeting regulations—they’re about boosting efficiency, reducing downtime, and creating a safer workplace. Materials like polycarbonate and HDPE offer impact resistance, chemical durability, and easy customization, making them essential for industrial safety. Due to their low maintenance and recyclability, polycarbonate and HDPE stand out as cost-effective, sustainable choices for any facility.
Gain Further Insights
Our experts will help you find the perfect materials to protect your workers, reduce risks, and enhance your operations. Contact one of our specialists for more information!
Get In Touch