A Thorough Review & Analysis
Engineering plastics are specialized materials designed to meet the demanding requirements of various industrial applications, offering superior mechanical and thermal properties compared to more common plastics. Selecting the right engineering plastic is vital, as each type provides exceptional benefits tailored to specific technical needs, such as strength, durability, heat resistance, and chemical stability.
In this comparison, we will focus on key types of engineering plastics—Polycarbonate, ABS, PEEK, Nylon, and Polypropylene—and their distinct characteristics for different applications.
This analysis will guide professionals in making informed decisions about which plastic best meets their projects' specific requirements, ensuring the best performance and cost-effectiveness.
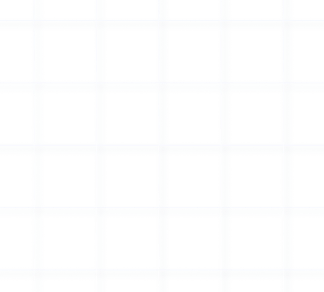
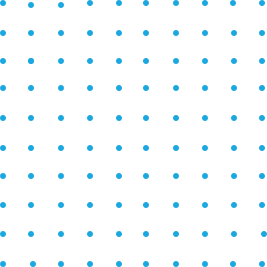
An Expert is just around the corner.
With over 100 years of combined product knowledge and industry experience, we are confident our plastics experts can help you find a solution for your application.
Heat Resistance and Thermal Properties
Each material's maximum service temperature and thermal degradation point dictate its effectiveness in environments from automotive engines to high-temperature electronics.
Polycarbonate: Due to its good heat resistance, polycarbonate can withstand temperatures up to 135°C. It is often used in automotive headlamp lenses and electronic housing.
ABS: This material functions well up to 100°C, making it suitable for automotive interior parts and appliances where lower heat resistance is sufficient.
PEEK: It excels with a service temperature of up to 250°C, proving it ideal for aerospace components and high-performance electronics due to its excellent high-temperature stability.
Nylon: It operates effectively up to 150°C and is commonly used in under-the-hood automotive parts and mechanical components that experience medium to high temperatures.
Polypropylene: It handles temperatures up to 130°C but is often selected for less heat-intensive applications like chemical tanks and indoor plumbing due to its lower thermal stability compared to other materials.
Strength and Durability
These materials offer different strengths, making them appropriate for specific uses ranging from safety applications to high-stress industrial components.
Polycarbonate (PC) | Acrylonitrile Butadiene Styrene (ABS) | Polyether Ether Ketone (PEEK) | Nylon | Polypropylene (PP) |
---|---|---|---|---|
Distinctive Qualities: High Impact Resistance, Good Tensile Strength | Distinctive Qualities: Excellent Impact Resistance, Moderate Tensile Strength | Distinctive Qualities: Exceptional Tensile Strength, High Fatigue Endurance | Distinctive Qualities: High Tensile Strength, Good Fatigue Endurance | Distinctive Qualities: Adequate Tensile Strength, Good Impact Resistance |
Uses: Best for safety equipment and bulletproof glass, where durability under impact is crucial | Uses: Ideal for consumer electronics and automotive parts, offering a good balance of durability and flexibility | Uses: The material of choice for aerospace and high-stress applications due to its superior strength and thermal stability | Uses: Commonly used in the manufacturing of gears and bearings, where long-lasting durability is needed | Uses: Suitable for less critical applications like piping and storage containers, where moderate strength is sufficient |
Substance and Environmental Resistance
The chemical resistance of these engineering plastics varies, influencing their suitability for environments exposed to chemicals, UV light, and moisture.
Polycarbonate (PC): It has good resistance to acids and bases but is sensitive to solvents such as acetone, which can cause damage. It is moderately resistant to UV but often requires additional coatings for reliable outdoor use in applications like outdoor lighting.
Acrylonitrile Butadiene Styrene (ABS): ABS resists water-based acids and alkalis well but is weak against many organic solvents. It's not typically suited for outdoor use without UV stabilization treatments, making it better for indoor applications like appliance casings.
Polyether Ether Ketone (PEEK): This plastic is resistant to a wide array of chemicals, including tough solvents, acids, and bases. PEEK is ideal for harsh environments like chemical processing or medical devices. It also handles UV exposure well, making it suitable for demanding outdoor aerospace and automotive applications.
Nylon: Nylon is generally good with fuels and oils but absorbs water, which can compromise its mechanical properties. It degrades with strong acids and bases and requires UV stabilization for outdoor use, such as sports equipment.
Polypropylene (PP): Highly resistant to chemicals and moisture, polypropylene is excellent for chemical containers and plumbing in harsh environments. It has moderate UV resistance, enhanced with additives for outdoor items like garden furniture or vehicle parts.
Electrical Insulation Capabilities
Engineering plastics' dielectric strength and electrical insulation properties are critical for determining their use in electrical and electronic applications. Each material offers unique features suitable for specific roles.
Polycarbonate (PC): Known for high dielectric strength and excellent insulation, it is ideal for circuit breaker housings and connectors. Its transparency also supports applications requiring visual part inspections.
Acrylonitrile Butadiene Styrene (ABS): ABS has good insulation properties and is used for the casings of power tools and electronics, where moderate insulation and durability are needed.
Polyether Ether Ketone (PEEK): This material stands out for its high dielectric strength and thermal stability, making it perfect for aerospace and automotive electronics that operate under extreme conditions.
Nylon: This product offers solid electrical insulation but is moisture-sensitive, making it suitable for insulators and cable ties in controlled environments.
Polypropylene (PP): Excellent for electrical insulation and high dielectric strength, polypropylene is used in high-voltage applications and large-scale electrical component production due to its affordability.
Cost and Manufacturing Considerations
Polycarbonate and ABS are generally more affordable and easier to process, making them cost-effective for large-scale consumer goods and automotive parts production.
While offering superior mechanical and thermal properties, PEEK comes at a higher cost, which can be justified in high-performance applications such as aerospace and medical devices, where durability under extreme conditions is critical.
Nylon offers a middle ground with good mechanical properties and moderate cost, which is suitable for applications like gears and bearings. Polypropylene is the most economical among these plastics, offering good chemical resistance and ease of processing, making it ideal for a wide range of consumer products and packaging solutions.
For large-scale production, ABS and Polypropylene often balance performance and cost, particularly where high volumes and low unit costs are necessary.
Compliance and Sustainability
Engineering meets stringent safety and regulatory standards for sensitive applications such as food contact and medical devices. PP and certain grades of PC are commonly used in food containers and medical devices, adhering to FDA regulations and international standards like ISO and ASTM, which are crucial for global market acceptance. PEEK is particularly valued in medical implants for its biocompatibility.
Additionally, the sustainability aspects of these materials, such as the high recyclability of PP and ongoing improvements in the recyclability of Nylon and ABS, reflect efforts to reduce environmental impacts.
Ready to Buy?
Whether you're involved in medical, food contact, automotive, or any other sector requiring dependable and compliant materials, Piedmont Plastics offers expert guidance and a wide range of options to ensure you find the perfect fit for your needs.
Find Out More
Contact our plastic specialists to enhance your projects with our top-tier plastics and benefit from our commitment to excellence.
Get In Touch