Containment Plastics: Safety Starts Here
Containment grade plastics are a critical component in the infrastructure of industries handling hazardous or sensitive materials. Their primary function is to contain, isolate, and prevent the release of substances that could threaten human health, equipment, or the environment.
As industries face increasing pressure to meet stricter environmental and safety regulations, the role of containment-grade materials has become more prominent. The selection of the appropriate plastic for containment is not a one-size-fits-all approach. It requires an understanding of chemical resistance, structural performance, temperature tolerance, and long-term reliability. Read on to learn more about the best containment-grade materials for your application!
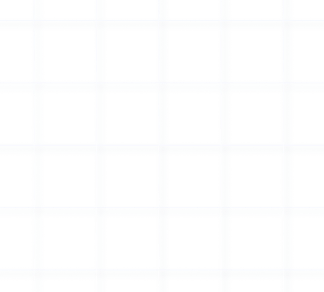
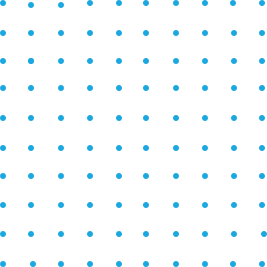
An Expert is just around the corner.
With over 100 years of combined product knowledge and industry experience, we are confident our plastics experts can help you find a solution for your application.
What is Containment Grade Plastic?
Containment grade plastics are engineered to provide superior physical and chemical barrier properties. These materials are designed to prevent the migration or leakage of hazardous substances, such as corrosive chemicals, fuels, or biologically hazardous materials. They are used in both primary containment, such as tanks or pipes that directly hold materials, and secondary containment systems designed to capture substances if the primary system fails.
Various federal and international regulatory bodies define standards for containment systems. These include the Environmental Protection Agency (EPA), Occupational Safety and Health Administration (OSHA), Department of Transportation (DOT), and Nuclear Regulatory Commission (NRC).
Additionally, organizations such as the National Fire Protection Association (NFPA) and the International Fire Code (IFC) have established guidelines to make sure that containment systems meet safety and fire-resistance standards. Compliance with these regulations requires that the materials used are durable and capable of performing under stress without failure.
Material Properties and Performance Requirements
To function effectively, container-grade plastics must possess a specific set of performance attributes. One of the foremost considerations is chemical resistance. These materials must withstand prolonged exposure to aggressive substances, including strong acids, bases, organic solvents, and oxidizing agents. Degradation due to chemical attack can compromise the structural integrity of containment systems, leading to leaks and failures.
Mechanical strength and impact resistance are equally important. Containment plastics often operate in industrial settings where mechanical stress, vibration, or accidental impacts can occur. Therefore, the material must absorb and distribute these forces without cracking or rupturing.
Thermal performance is another key factor. Many industrial environments involve elevated or fluctuating temperatures, requiring materials that support dimensional stability and mechanical performance over a broad temperature range.
Moisture resistance, impermeability, and resistance to environmental stress cracking are essential in outdoor or high-humidity applications. In such conditions, the plastic must resist swelling, delamination, and other forms of degradation. Additionally, UV resistance may be necessary for outdoor applications to prevent brittleness and discoloration caused by prolonged exposure to sunlight.
Common Containment Grade Plastics and Their Applications
When selecting materials for containment-grade applications, it’s fundamental to know the strengths and limitations of each plastic. Different environments and substances require specific properties, such as chemical resistance, mechanical strength, or thermal stability, to guarantee long-term safety and compliance.
Here’s a closer look at the most commonly used containment-grade plastics and their applications:
High-Density Polyethylene (HDPE): A top choice for many containment systems, HDPE combines strength, chemical resistance, and low permeability. It’s ideal for use in containment liners, chemical storage tanks, and pipe systems. Its UV resistance also makes it reliable for outdoor applications.
Ultra-High Molecular Weight Polyethylene (UHMW): Known for its exceptional wear resistance, UHMW performs well in high-abrasion environments. It’s commonly used in secondary containment systems and industrial applications where impact and mechanical stress are frequent.
Polyvinyl Chloride (PVC) and Chlorinated PVC (CPVC): These materials are valued for their excellent corrosion resistance and ability to withstand high temperatures. They are often used in chemical processing plants for piping, valves, and tank systems.
Polypropylene: This plastic offers a good balance of chemical resistance and cost efficiency. It’s often selected for moderate-duty containment systems, such as intermediate bulk containers, chemical bins, and secondary containment units.
Polytetrafluoroethylene (PTFE / Teflon®): For applications involving aggressive chemicals and high temperatures, PTFE is the go-to material. Its superior non-reactivity and thermal resilience make it suitable for the most demanding containment environments. However, due to its higher cost, it is typically reserved for specialized or serious systems.
Engineering Considerations in Material Selection
Choosing the right containment grade plastic requires a comprehensive evaluation of several technical parameters. Chemical compatibility should be verified using reference tables or through direct testing, as even small concentrations of certain chemicals can cause degradation in some plastics over time. Engineers must also assess load-bearing requirements, as containment structures must support large volumes of liquid under pressure.
Thermal expansion, welding capabilities, and ease of fabrication are critical in installation and long-term maintenance planning. Plastics that are difficult to weld or fabricate may lead to higher installation costs or increased risk of failure due to poor joint integrity. Furthermore, environmental conditions such as exposure to UV radiation, sub-zero temperatures, or mechanical abrasion should be considered when specifying materials for outdoor or mobile applications.
Regulatory Compliance and Industry Standards
Regulatory compliance is a non-negotiable aspect of containment systems. In the U.S., EPA regulations under the Resource Conservation and Recovery Act (RCRA) stipulate requirements for secondary containment of hazardous waste. OSHA mandates containment measures to protect workers from chemical exposure, while DOT regulations govern the transportation of dangerous materials. Adherence to these standards is essential for safety and avoiding legal liabilities and costly fines.
Selected materials must often be certified to meet specific material standards such as ASTM specifications, FDA compliance (for food or pharmaceutical applications), or military-grade requirements for defense applications. In addition, documentation, traceability, and material certifications are often necessary for procurement and quality assurance.
Sourcing for Containment Grade Plastic Materials
At Piedmont Plastics, we offer a comprehensive selection of containment grade plastics designed to meet the highest safety, durability, and regulatory compliance standards. Our product range includes HDPE, UHMW, CPVC, polypropylene, and PTFE, among others, and they are available in various sheet, rod, and custom-fabricated forms. We understand that each application has unique demands, so our expert team works closely with customers to specify and source the right material for the job.
With a nationwide distribution network, Piedmont Plastics guarantees the timely delivery of high-quality materials, supported by expert guidance and fabrication services. Whether constructing a chemical processing plant, developing a waste containment system, or upgrading safety features in a high-risk environment, Piedmont Plastics is your trusted partner in achieving dependable, code-compliant containment solutions.
How Can We Serve You?
Let Piedmont Plastics help you make the right choice for your project, your people, and the environment. Contact us now to learn more!
Get In Touch