Marine environments are some of the toughest on materials. Saltwater corrodes metal. Intense sunlight breaks down unprotected surfaces. Constant impacts from waves, docks, and equipment add even more stress. In these conditions, only the most resilient materials last, and marine-grade plastics are designed to do exactly that.
Read on to learn more about how these plastics excel in marine environments!
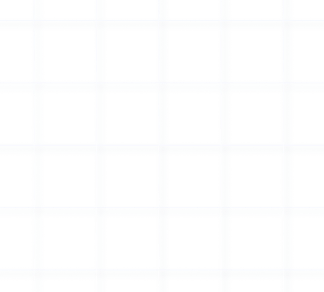
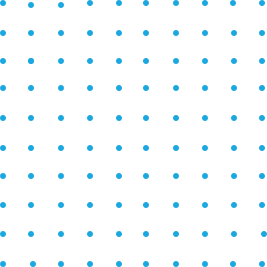
An Expert is just around the corner.
With over 100 years of combined product knowledge and industry experience, we are confident our plastics experts can help you find a solution for your application.
Marine-Grade Plastics vs. the Elements
When engineers talk about strength in marine applications, they look beyond simple load capacity. The real test is how a material holds up against water, sun, and physical wear over time. Marine-grade plastics are specially engineered to outperform wood, metal, and general-purpose plastics by resisting the three most common threats: saltwater corrosion, UV damage, and mechanical impact.
Saltwater does not affect these plastics. They don’t rust, swell, or deteriorate, making them a dependable choice for long-term use in or near seawater. Sun exposure is another major concern. While many materials weaken or fade under UV radiation, marine-grade plastics contain stabilizers that block harmful rays. This prevents cracking and brittleness, allowing them to maintain strength and appearance for years.
Physical impact is the third critical factor. Marine-grade plastics are tough and flexible enough to absorb shock without cracking, whether it’s from a crashing wave or contact with gear or docks.
These combined properties make marine plastics uniquely durable. Even in full exposure, they hold up with little to no maintenance. Now let’s explore some of the most trusted marine materials in use today.
The Unsinkable Workhorse
High-Density Polyethylene (HDPE) is one of the most trusted plastics in marine applications, and for good reason. Among other advantages, it is lightweight, extremely durable, and built to perform in demanding environments without cracking, rotting, or corroding. Its physical properties make it a top choice for docks, hulls, and structural components that face regular exposure to water and impact.
HDPE is especially effective in marine settings because of its:
Flexibility under impact: HDPE can absorb force and flex without breaking, making it ideal for parts that take frequent hits, like fender boards and bumpers.
Complete moisture resistance: It doesn’t absorb water, swell, or support mold, even when submerged long-term.
UV stability: UV-resistant formulations, especially black HDPE with carbon black, protect against sun damage and material breakdown.
Natural buoyancy: HDPE floats, perfect for floating docks and safety-critical applications.
Lightweight, Rigid, and Built to Last
When your project requires both strength and lightweight, marine-grade Polyvinyl Chloride (PVC) delivers. It’s a reliable material for everything from interior panels and cabinetry to seat bases and structural components, especially where moisture and UV exposure are concerns.
Unlike plywood, marine-grade PVC won’t swell, warp, or delaminate. In particular, expanded PVC foam sheets are valued for their rigidity, smooth surface, and ease of fabrication. They provide long-lasting performance in both structural and decorative applications.
Key advantages of marine-grade PVC include:
Water resistance: PVC won’t absorb moisture, making it ideal for wet or humid environments.
UV stability: Formulated with UV inhibitors, it resists yellowing, cracking, and brittleness under sun exposure.
Chemical durability: It stands up to salt, oil, and fuel, making it suitable for high-exposure areas.
Fire resistance: Naturally flame-retardant, marine-grade PVC is safe to use near engines and electronics.
Lightweight and low maintenance: Easier to work with and maintain than wood or metal, marine-grade PVC offers comparable strength in many applications.
The Strong, Stable Backbone
Acrylonitrile Butadiene Styrene (ABS) offers a powerful combination of rigidity and toughness, making it a go-to material for demanding marine applications. Whether outfitting a helm console, mounting electronics, or fabricating enclosures, ABS provides reliable structural integrity without the weaknesses of wood or metal.
Its performance also holds up under the pressures of marine use, resisting impact, vibration, and extreme temperature swings while keeping its form and finish over time.
Marine-grade ABS is favored for several key reasons:
High Impact Strength | ABS withstands vibration and mechanical stress without cracking or breaking. |
---|---|
Excellent Dimensional Stability | This material maintains its shape even in fluctuating temperatures and harsh sunlight. |
Water Resistance | Minimal absorption prevents swelling, softening, or distortion in wet conditions. |
UV Protection | Formulations with stabilizers ensure durability above deck and in sun-exposed areas. |
Structural Support | High-density ABS boards make ideal replacements for wood in backing plates and transom mounts, offering comparable strength without rot or splitting. |
Why Use Marine-Grade Plastic Rather Than Metal or Standard Plastic?
At first glance, traditional materials like metal or untreated plastic may seem adequate for marine builds. However, they fall short in real-world conditions, especially over time.
Metals, for example, are vulnerable to saltwater corrosion and often require protective coatings, sacrificial anodes, or constant maintenance. While lighter than steel, even aluminum can suffer from galvanic corrosion and fatigue at welded joints. Additionally, metals add significant weight to marine structures, affecting fuel efficiency and handling.
Standard plastics may seem like a lighter, lower-cost alternative, but they’re typically not built for the sun, salt, and stress of marine use. Most lack the UV stabilizers or antifungal properties needed to survive long-term. As a result, they can become brittle, fade, crack, or deform within a season, especially under direct UV exposure or saltwater immersion.
Trusted Materials, Trusted Supplier
At Piedmont Plastics, we realize that marine performance isn’t optional: it’s essential. That’s why we supply marine-grade materials engineered to perform in the harshest conditions.
We offer a wide selection of HDPE sheets and boards, expanded PVC foam panels, and ABS sheet materials available in multiple thicknesses, finishes, and colors. Our team can also provide cut-to-size services and expert material guidance to match your application needs.
From cup holders to marine enclosures, we support engineers and fabricators with the highest-quality marine-grade plastics on the market.
Ready to Build Something That Lasts?
Whether you're designing a lightweight hull component, retrofitting a dock, or fabricating custom marine enclosures, don't settle for materials that degrade or rust. Choose plastics that are purpose-built for life on the water.
Dive Deeper
With Piedmont Plastics, you’re not just choosing materials, you’re choosing performance that lasts above and below the waterline. Contact us today for more information!
Discover More