Corrosion-Resistant Plastics in Semiconductor Chemical Storage
The semiconductor industry relies on highly controlled environments and ultrapure chemicals for manufacturing processes such as wafer etching, cleaning, and deposition. Chemical storage solutions must keep the integrity of these substances while preventing contamination and corrosion.
Corrosion-resistant plastics offer a superior alternative to metals due to their inertness, lightweight properties, and ability to withstand aggressive chemical exposure. Selecting the right anti-corrosive plastic is critical for ensuring process stability, worker safety, and long-term equipment performance.
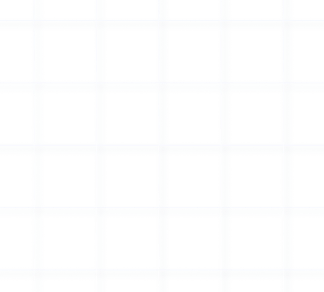
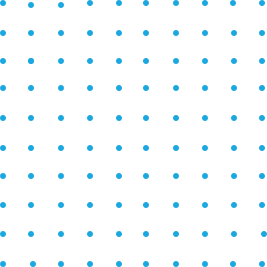
An Expert is just around the corner.
With over 100 years of combined product knowledge and industry experience, we are confident our plastics experts can help you find a solution for your application.
Major Factors in Choosing Anti-Corrosive Plastics
Selecting the right plastic for chemical storage requires careful consideration of several key factors to ensure durability, safety, and performance.
The material must resist harsh chemicals, withstand extreme temperatures, and maintain structural integrity over time.
Serious considerations include:
Chemical Resistance: Must withstand high-concentration acids, bases, and organic solvents without degrading.
Thermal Stability: Needs to perform under high operating temperatures, especially in semiconductor fabrication environments.
Mechanical Durability: Should resist stress cracking, abrasion, and impact for long-term tank integrity.
Low Permeability and Non-Leaching: Prevents contamination by maintaining chemical purity and protecting ultrapure water.
Electrical Insulation and Static Dissipation: Helps prevent electrostatic discharge (ESD) that could damage sensitive semiconductor components.
Top Anti-Corrosive Plastics for Chemical Storage
Using the right plastic for semiconductor chemical storage is crucial to ensure long-term durability, chemical purity, and safety. Several high-performance plastics stand out for their exceptional resistance to corrosion and ability to withstand extreme conditions, including:
Polytetrafluoroethylene (PTFE): Known for its unmatched chemical resistance, PTFE withstands nearly all acids, bases, and solvents while remaining stable from -200°C to 260°C. Its non-stick properties, low friction, and superior electrical insulation make it ideal for chemical transport lines, tank linings, and semiconductor processing components.
Polyvinylidene Fluoride (PVDF): Highly resistant to aggressive acids like hydrofluoric acid, PVDF can operate at temperatures up to 150°C. With excellent mechanical strength, UV resistance, and high purity, it is widely used in chemical storage tanks, ultrapure water systems, and semiconductor process piping.
Ethylene Chlorotrifluoroethylene (ECTFE): Designed for harsh environments, ECTFE offers strong resistance to high-concentration acids and bases while functioning efficiently between -76°C to 148°C. Its low permeability, impact resistance, and easy fabrication make it ideal for corrosion-resistant linings in chemical tanks and cleanroom applications.
Polypropylene (PP): A budget-friendly choice with good resistance to dilute acids, bases, and organic solvents. With a maximum operating temperature of 100°C, PP is lightweight, easy to fabricate, and commonly found in chemical storage tanks, fume hoods, and lab equipment. While not as chemically resistant as PTFE or PVDF, it is still a reliable choice for moderate applications.
High-Density Polyethylene (HDPE): Offering solid resistance to acids and solvents, HDPE is valued for its impact strength, environmental stress crack resistance, and affordability. Though its temperature limit is lower at 55°C, it is commonly used for chemical transport containers, waste storage tanks, and piping systems.
*Data is approximate and may be based on averages. Contact your local Piedmont Plastics sales representative for specific product specifications.
Rotational Molding and Fabrication Techniques
To maximize durability and chemical resistance, rotational molding is commonly employed to fabricate seamless, high-purity plastic tanks. This process ensures uniform wall thickness, eliminating weak points where chemical exposure could lead to failure. Rotational molding also prevents leaks and contamination by producing seamless containers, making it particularly effective for high-performance fluoropolymer resins such as PFA, PTFE, and PVDF.
One of the major advantages of rotational molding is its ability to create tanks with no seams or joints, thereby reducing the risk of chemical leakage. This process also allows for high chemical resistance and customization options, such as sensor integration, fittings, and complex geometries custom-made to semiconductor applications. While alternative fabrication methods such as extrusion welding and injection molding are used for specialized components, they may introduce seams that require secondary processing to keep chemical integrity.
Which Plastic is Best for Your Application?
Plastic Type | Chemical Resistance | Max Operating Temp (°C) | Best Use Cases |
---|---|---|---|
PTFE | Excellent | 260°C (500°F) | Extreme chemical resistance, high-purity storage |
PVDF | Excellent | 150°C (302°F) | Semiconductor tanks, ultrapure water systems |
ECTFE | Excellent | 148°C (298°F) | High-concentration acids and aggressive chemicals |
Polypropylene | Good | 100°C (212°F) | Cost-effective storage for moderate acids |
HDPE | Good | 55°C (131°F) | Impact-resistant storage for general chemicals |
Where Anti-Corrosive Plastics Are Used
Anti-corrosive plastics play a fundamental role in various aspects of semiconductor manufacturing. Chemical storage tanks made from PTFE, PVDF, or ECTFE ensure the safe containment of high-purity chemicals used in etching, deposition, and cleaning processes. These materials also contribute to ultrapure water systems by preventing ion leaching and maintaining the stringent purity requirements necessary for semiconductor fabrication.
In wet processing equipment, plastics resistant to corrosion, such as polypropylene and HDPE, are used for chemical etching, cleaning, and coating applications. Piping and fluid distribution systems rely on high-performance plastics like PVDF and ECTFE to transport aggressive chemicals without the risk of corrosion or leaching. Additionally, cleanroom environments benefit from non-leaching, low-particulate plastics to minimize contamination risks during semiconductor processing.
What Does The Future Hold?
As semiconductor manufacturing advances, new materials and fabrication techniques are emerging to further enhance the performance of anti-corrosive plastics. Recent developments in fluoropolymer coatings offer enhanced protective linings with increased chemical resistance. There is also a growing interest in sustainable and recyclable high-performance plastics, aimed at reducing the environmental impact of semiconductor production.
Automation in plastic tank manufacturing is another key trend, improving precision and efficiency in large-scale production. With the increasing demand for high-purity and corrosion-resistant solutions, innovations in polymer chemistry and manufacturing technology continue to push the boundaries of what plastics can achieve in semiconductor chemical storage applications.
Looking For More Information?
Picking the optimal corrosion-resistant plastic for semiconductor chemical storage depends on specific process requirements, including chemical exposure, temperature range, mechanical durability, and purity standards. PTFE is the best choice for extreme chemical resistance and high-temperature applications. For cost-effective solutions, polypropylene and HDPE provide reliable performance in moderate conditions.
We specialize in providing high-performance plastic solutions tailored to your semiconductor storage needs. Our experts can assist you with selecting the right materials and fabrication techniques to enhance process stability, ensure long-term durability, and meet the stringent demands of high-purity chemical containment.
Discover More Insights
Get in touch with us today to find the best plastic solution for your application!
Contact Us