Why Plastics Are the Future of Bus Design and Engineering
In mass transit, durability, efficiency, and safety aren’t optional; they’re fundamental. Every part must hold up against constant vibration, moisture, harsh cleaning chemicals, and wide temperature swings. At the same time, manufacturers can’t sacrifice aesthetics, passenger comfort, or compliance with strict safety standards.
Today’s bus manufacturers increasingly turn to advanced plastic materials to meet these demands. As a result, thermoplastics and composites are becoming increasingly smarter and more versatile alternatives to traditional materials, such as metal, wood, and fiberglass. At Piedmont Plastics, we’re proud to support this shift by helping OEMs and suppliers access the high-performance plastics they need to build buses that are lighter, stronger, more efficient, and built to last.
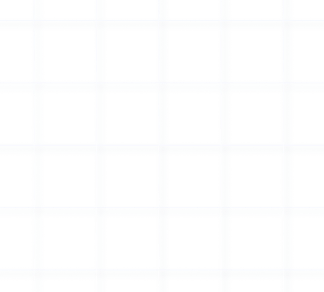
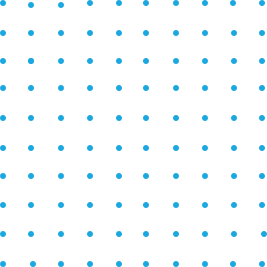
An Expert is just around the corner.
With over 100 years of combined product knowledge and industry experience, we are confident our plastics experts can help you find a solution for your application.
Why Plastics Are the Smart Choice for Bus Manufacturing
Thermoplastics offer a powerful combination of advantages that address the exact needs of the bus industry. One of the most obvious benefits is weight reduction. Plastics can be up to 6 times lighter than steel and half the weight of aluminum. That kind of weight savings adds up fast across a vehicle’s frame, panels, and interior components, improving fuel economy or battery range, reducing brake and tire wear, and enabling manufacturers to meet emissions or electrification goals more easily.
Plastics are also resistant to corrosion, rot, and chemicals. Unlike metal, they won’t rust; unlike wood, they won’t warp, split, or absorb moisture over time. These qualities translate into longer service life, fewer replacements, and lower maintenance costs, especially for fleets operating in harsh conditions.
They also offer impressive impact strength, dimensional stability, and surface durability. Many plastics can flex on impact instead of denting or shattering, making them ideal for high-traffic public spaces.
And finally, plastics deliver unmatched design flexibility. They can be formed into sleek curves, molded with built-in textures, and produced in virtually any color without the need for painting. That freedom unlocks better aesthetics, faster manufacturing, and even easier branding for transit agencies.
Where Plastics Work on the Bus
Modern buses are filled with plastic components that contribute to safety, comfort, and efficiency, often in places passengers don’t even notice. These materials replace heavier, more corrosion-prone options like metal, glass, and wood, while offering added durability, flexibility, and ease of maintenance.
Here are some of the most common areas where plastics are used in bus construction:
Windows and Windshields: Up to 250 times stronger than glass and much lighter, polycarbonate is commonly used in driver shields, skylights, and side glazing to improve impact resistance and safety.
Interior Wall Panels and Trim: Typically formed from ABS, PVC alloys, or KYDEX®, these materials are easy to thermoform into custom shapes, offer flame resistance, and can be pre-colored and textured, with no paint required.
Seating Components: ABS and polypropylene are used for molded seat shells, tray tables, and armrests. These materials reduce seat weight, enhance passenger comfort, and simplify cleaning.
Partitions and Driver Barriers: Made from clear acrylic or polycarbonate, these dividers provide visibility and protection. Ideal for high-contact environments, they’re durable, vandal-resistant, and won’t yellow or scratch easily.
Flooring Systems: Plastic composite subfloors and non-slip vinyl coverings withstand heavy foot traffic, moisture, and cleaning chemicals. In addition, they’re safe, durable, and easy to maintain.
Exterior Panels: Items like bumpers, fairings, and wheel covers are often built with plastic composites. These parts are lightweight, corrosion-resistant, and easily replaceable, helping reduce downtime and maintenance.
How Plastics Are Made Bus-Ready
Producing plastic components for transit vehicles usually involves thermoforming or injection molding, two manufacturing processes perfectly suited for transportation applications.
Thermoforming heats flat plastic sheets until they become pliable, then molds them into precise shapes over a form. This process is ideal for large, lightweight parts like wall panels, seat backs, and exterior skins. Thermoforming tools are relatively low-cost and quick to produce, making them perfect for medium-volume runs or customized designs.
Injection molding, on the other hand, is used for smaller, more detailed parts. Plastic pellets are melted and injected into molds to create intricate components like handles, housings, vents, or mirror enclosures. The finish is consistently high quality and has excellent repeatability, making it great for parts used across multiple vehicle models or fleets.
These processes enable efficient production and allow engineers to consolidate parts, reduce fasteners, and integrate mounting features directly into the design, resulting in quicker and cleaner assembly.
Fuel Efficiency, Safety, and Compliance in Every Part
Beyond weight savings, plastics are necessary to make buses safer and more efficient. Because they’re naturally vibration-dampening, plastic panels help reduce road noise and create quieter, more pleasant interiors. Their non-conductive properties also mean interior surfaces stay more temperature-neutral, which can contribute to climate control efficiency.
From a safety standpoint, many transportation-grade plastics meet strict flammability and smoke emission standards, most notably FMVSS 302 and FTA Docket 90-A. These regulations ensure materials used inside passenger cabins don’t contribute to the spread of fire or harmful smoke during an emergency.
Materials like KYDEX®, flame-rated ABS, and polycarbonate are engineered to pass these tests while delivering impact resistance, clarity, and flexibility. For bus OEMs, that means peace of mind and easier certification.
Backed by Expertise
Our goal is to make sourcing the right plastic solutions simple, fast, and effective for OEMs and engineers. We offer one of the industry’s most extensive inventories of thermoplastics and composites, including polycarbonate, acrylic, ABS, PVC, HDPE, PETG, KYDEX®, and more. These materials come in numerous grades and finishes and meet critical standards for flame resistance, UV stability, impact strength, and chemical durability.
Here’s how we help streamline your production:
-
📚 Material Expertise
Our team works directly with your engineers to match each application with the ideal plastic, whether it needs to meet Docket 90-A, FMVSS 302, or stand up to years of daily use.
-
📋 Customized Solutions
We provide cut-to-size materials, fabrication guidance, and recommendations to optimize performance and reduce waste.
-
🖇️ Reliable Supply Chain Support
We keep your production schedule on track with local inventory and just-in-time delivery.
-
📞 Responsive Service
Whether you need a one-off sample or ongoing supply for a full fleet, we’re ready to help.
Let’s Move Forward Together
The future of mass transit is lightweight, safe, efficient, and smartly designed. In many ways, plastics are making that future possible.
Whether you’re prototyping a new model or improving an existing line, Piedmont Plastics is here to help you switch from old-school materials to high-performance plastics that save time, money, and energy. Contact us for more information!
Driving Innovation Forward
Let’s keep transportation moving smarter and safer. Get in touch with us today!
Find Out More