In today’s automotive vehicles, exterior body panels, interior components, and many internal mechanics are almost entirely made up of plastic materials. However, plastics have been a part of car manufacturing since 1907 when Leo Baekeland invented Bakelite, a synthetic plastic. Bakelite was lightweight, durable, non-conductive, and heat resistant, making it perfect for early car components such as instrument panels, control surfaces, and specific engine parts.
While Bakelite may no longer be used in automotive manufacturing, it has been replaced by an impressive selection of high-performance plastics that are helping shape the future of transportation. Parts made with high-performance plastics significantly improve a vehicle’s safety and reliability. To understand how this is all happening, it’s essential to know the plastics involved.
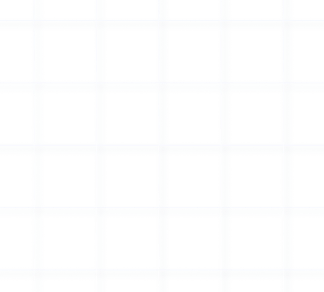
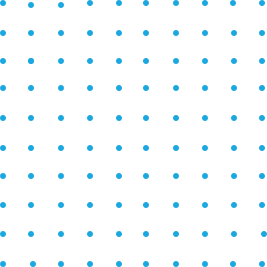
An Expert is just around the corner.
With over 100 years of combined product knowledge and industry experience, we are confident our plastics experts can help you find a solution for your application.
Here’s a rundown of today's most popular plastics in car components and how they’re used:
Plastics Commonly Used In Auto Parts
Plastics are a choice option for vehicle makers today because they are lightweight and inexpensive. Weight reduction appeals to the consumer’s desire for fuel efficiency, and plastic, in general, is corrosion-resistant and durable, which appeals to safety concerns. Plastics also provide significant design flexibility, making them more practical and inexpensive than metal.
To ensure that the materials used for manufacturing are both enduring and compliant, automotive manufacturers must adhere to a stringent set of industry requirements. This procedure is known as the material qualification process, and all plastics used in automobile manufacturing must undergo it.
As a result, the plastics found in cars are strong, reliable, and resistant to many harsh conditions. Plastics often used in car manufacturing include:
1) Polypropylene
Polypropylene is the most common plastic found in vehicle manufacturing. A thermoplastic polymer, it can easily be formed into almost any shape. It has excellent chemical resistance and heat resistance, and is frequently used in car bumpers, gas canisters, and carpet fibers.
Polypropylene is also a more economical alternative to expensive plastics of similar strength and durability, which helps drive down the cost of manufacturing.
2) Polycarbonate
Like polypropylene, polycarbonate is known for its impact resistance, which is why you’ll find it used in headlamp lenses and car fenders. Polycarbonate is highly weather-resistant and can withstand everything from heat and cold to rain and snow. In addition, polycarbonate’s lightweight features lower an automobile's overall weight, enhancing its performance and fuel economy.
3) PVC Plastic
PVC (polyvinyl chloride) is a flame-resistant material that can be shaped into flexible and stiff components. Due to its formability and sleek appearance, PVC is another popular material used in automobile interiors—particularly for dashboards, consoles, door coverings, and other interior body elements.
4) ABS Plastic
Like PVC, ABS (acrylonitrile butadiene styrene) plastic has an attractive, smooth finish and is frequently used to make dashboards and steering wheel coverings. In addition, ABS sheet is highly durable and heat resistant. Because it can absorb and redistribute energy during a collision, it’s a popular material when designing a vehicle for passenger safety.
5) Polyethylene
Polyethylene excels in components that require moisture resistance at a relatively low cost but also feature high-impact resistance, low density, and durability. Polyethylene is most often used for glass-reinforced car bodies and electrical insulation.
6) Nylon 6/6
Nylon 6/6 is a versatile nylon that has excellent wear resistance and is used to fabricate parts through both molding and extrusion techniques. In addition, it is frequently used in weatherproof coatings and is favored for its durability, affordability, and stability.
Choosing the Right Materials For the Job
The proper material selection for an automotive application can make a big difference in whether a vehicle is built to last, be fuel-efficient, and serve the consumers’ needs.
The plastics discussed above are only a sample of the wide range of plastics available for vehicle manufacturing. While these may be the most commonly used for making car components, vehicles come in many shapes and sizes. In addition, they are designed for various purposes, from simple transportation to hauling cargo, performing construction, and serving as emergency vehicles. That’s why it’s essential to use suitable plastic for the job.
Unsure Where To Start?
Contact the materials experts at Piedmont Plastics to help you determine what plastic will best service your manufacturing project!
Contact Us